New FRP Slipwalls Make Jacksonville Ferry Terminals A Soft Landing Corrosion Resistant - Passenger Friendly - Long Life Cycle
In the late 1800s, ferry service across the St. Johns River probably consisted of little more than a large wooden raft pulled by cables—its’ passengers people, animals and wagons.
Today the St. Johns River Ferry moves cars and passengers back and forth between Mayport and Fort George Island. The 0.9 mile voyage departs every half hour.
The Jacksonville Transportation Authority (JTA) secured funding for upgrades that included the fender slipwalls last year and took over operation of the St. Johns River Ferry in March 2016.
Aggressive currents and strong winds can make berth operations very difficult. The JTA needed energy absorbing guidewalls to address these challenging conditions.
The existing steel and concrete fender wall guiding the ferry into its slip was repeatedly subjected to hard hits. Steel and concrete are by nature very stiff resulting in hard landings which sometimes resulted in damage to the vessel and the guidewall
and compromised passenger safety.
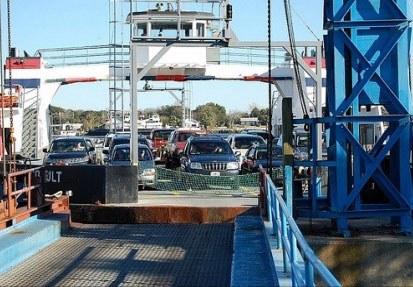
The JTA considered different alternatives with the primary goal to find a low maintenance fender slipwall system that would also provide greater energy absorption. Durability, flexibility, low maintenance and corrosion resistance made
FiberPILE the material of choice. The energy absorbing system reduces fender wall damage and improves safety and comfort, allowing passengers to enjoy the ride.
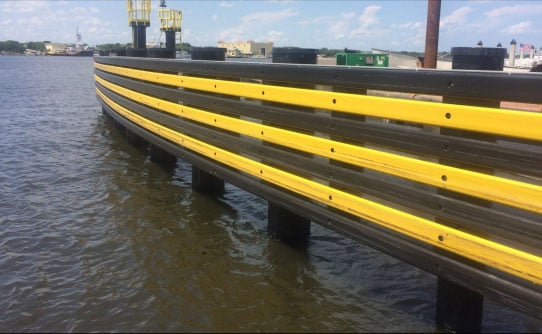
The new FRP slipwalls use a combination of 24-inch and 36-inch diameter FiberPILEs at lengths up to 100 feet. The wales are comprised of high strength composite timbers to distribute the impact loads to the piles. FRP channels splice the timbers along their lengths. The timbers are bolted to the piles.
FiberPILE — For Superior Energy Absorption
The Benefits:
- High Strength
- Superior Energy Absorption
- Recoverable Deflection
- No Maintenance
- Corrosion Resistant
- Hollow Construction (No Fill Required)
- Lightweight
- Low Driving Friction
- Dimensionally Stable
- Non-Magnetic
- High Impact Resistance
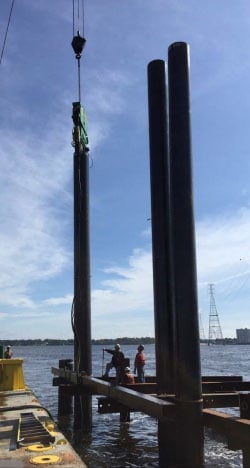
FiberPILE large diameter pilings are constructed using high-strength, directional fiberglass materials and a resin system formulated to withstand the most corrosive environments. The combination results in a maintenancefree piling product that is ideal for protecting structures from the impact of barges and ships.
Standard FiberPILE diameters range from 24 inches to 48 inches and can be fabricated in continuous lengths up to 100 feet. Because FiberPILE uses fewer, large diameter pipe piles, installation costs are reduced.
FiberPILE products can be driven with conventional pile driving equipment including both impact and vibratory hammers. FiberPILE can be cut, drilled, and connected using standard tools and hardware.
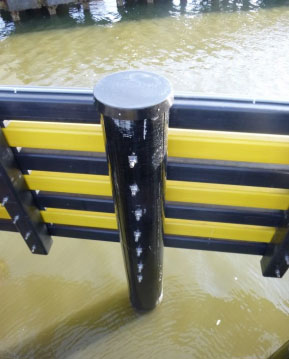
FiberPILES are driven into hard soils including wood piles from previous installations. Composite timbers bolt to the piles and distribute impact loads to the piles. Caps cover the hollow piles and also become the base for navigation lights.