OUR TECHNOLOGY
Composite Manufacturing Capabilities
The Creative Composites Group provides customer-focused engineered solutions using fiberglass/fiber reinforced polymer composite materials that are lightweight, corrosion-resistant and durable.
Innovative design and manufacturing expertise create products that make customer systems bigger, better and longer-lasting. Introducing the Creative Composites Group of companies to provide customers with a greater array of products, services and capabilities to ensure the optimal solution for any project.
The combined manufacturing capabilities of CCG encompass the primary processes for fabricating high-performing FRP composite structures. Whether requiring tight tolerances or big parts, the Group has the right manufacturing process to meet your requirements. Anything from 30 mils to 100 feet.
Being experts in all these processes enables CCG to select the process that delivers the optimum combination of cost, performance and quality. CCG considers parameters including quantity, size, tolerance, structural requirements to provide the best value.
PULTRUSION
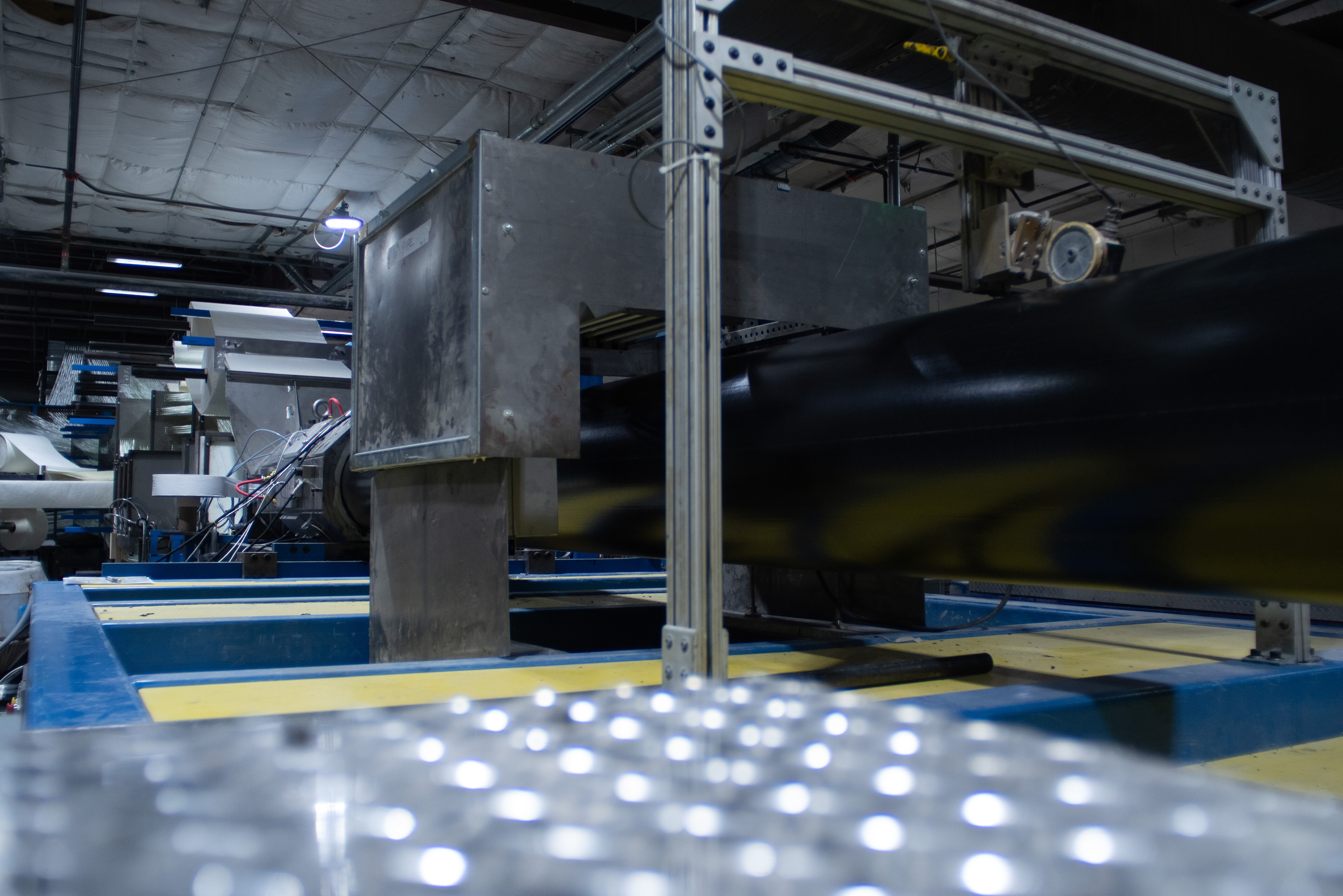
VACUUM INFUSION
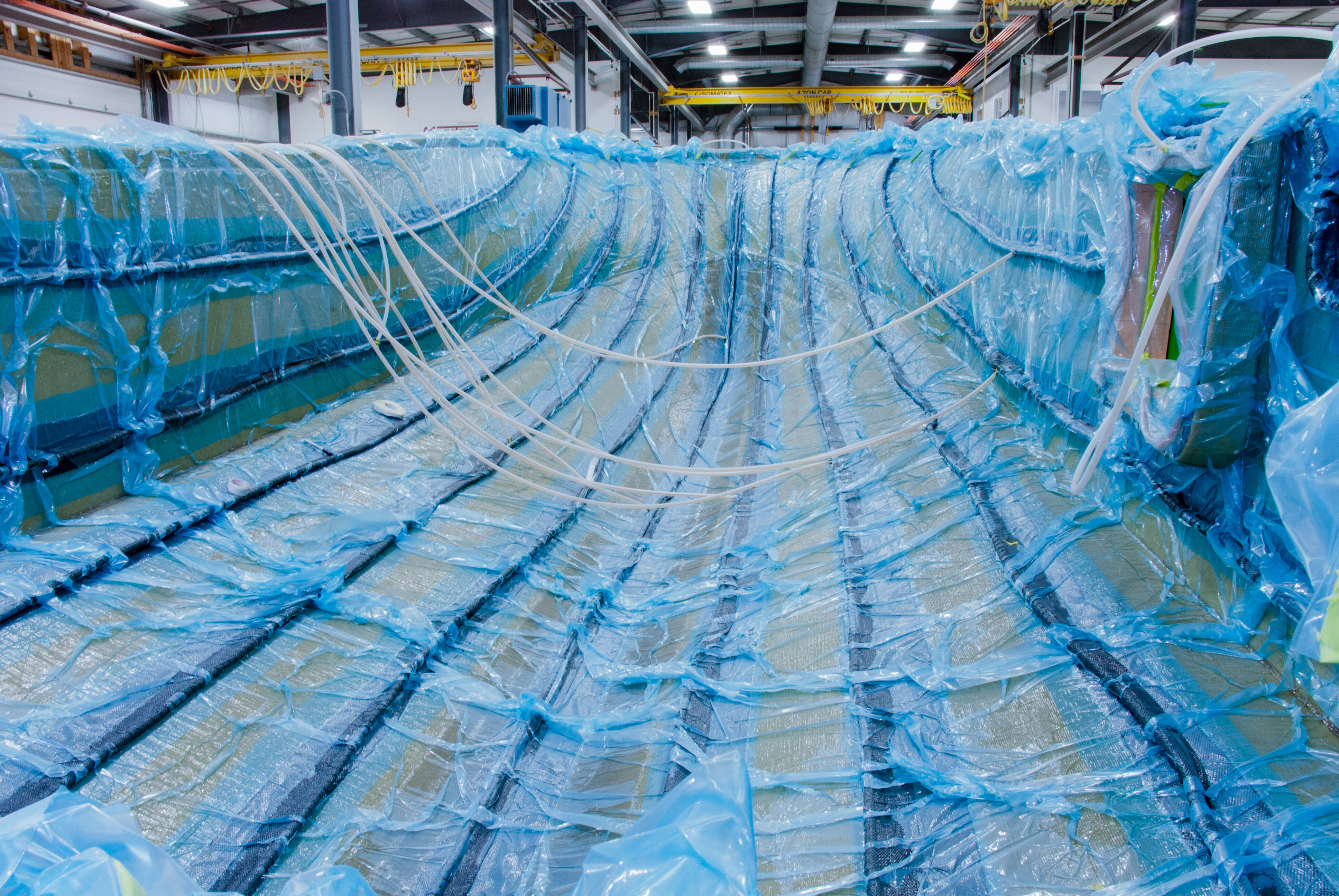
FILAMENT WINDING
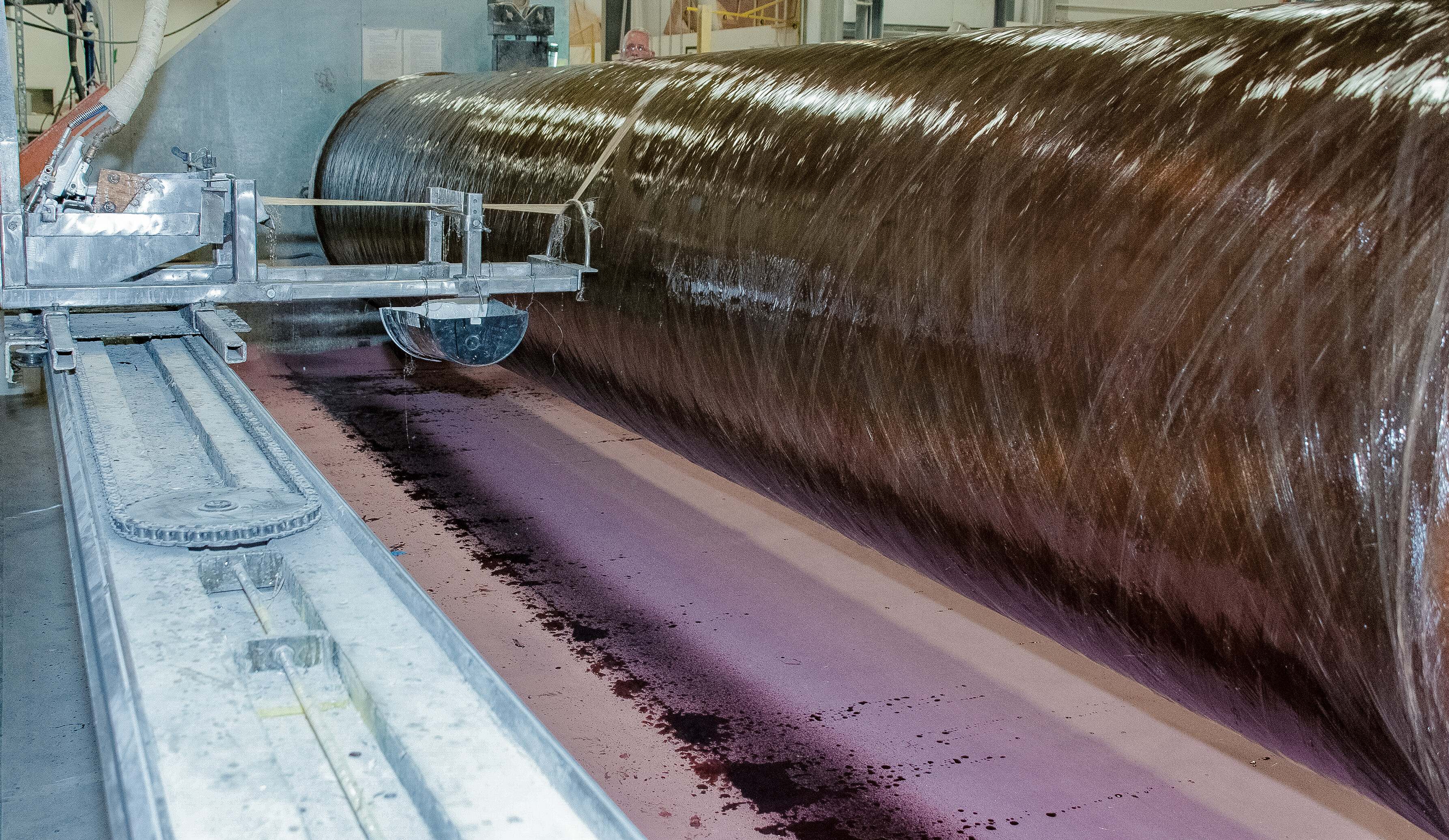
CONTINOUS LAMINATION
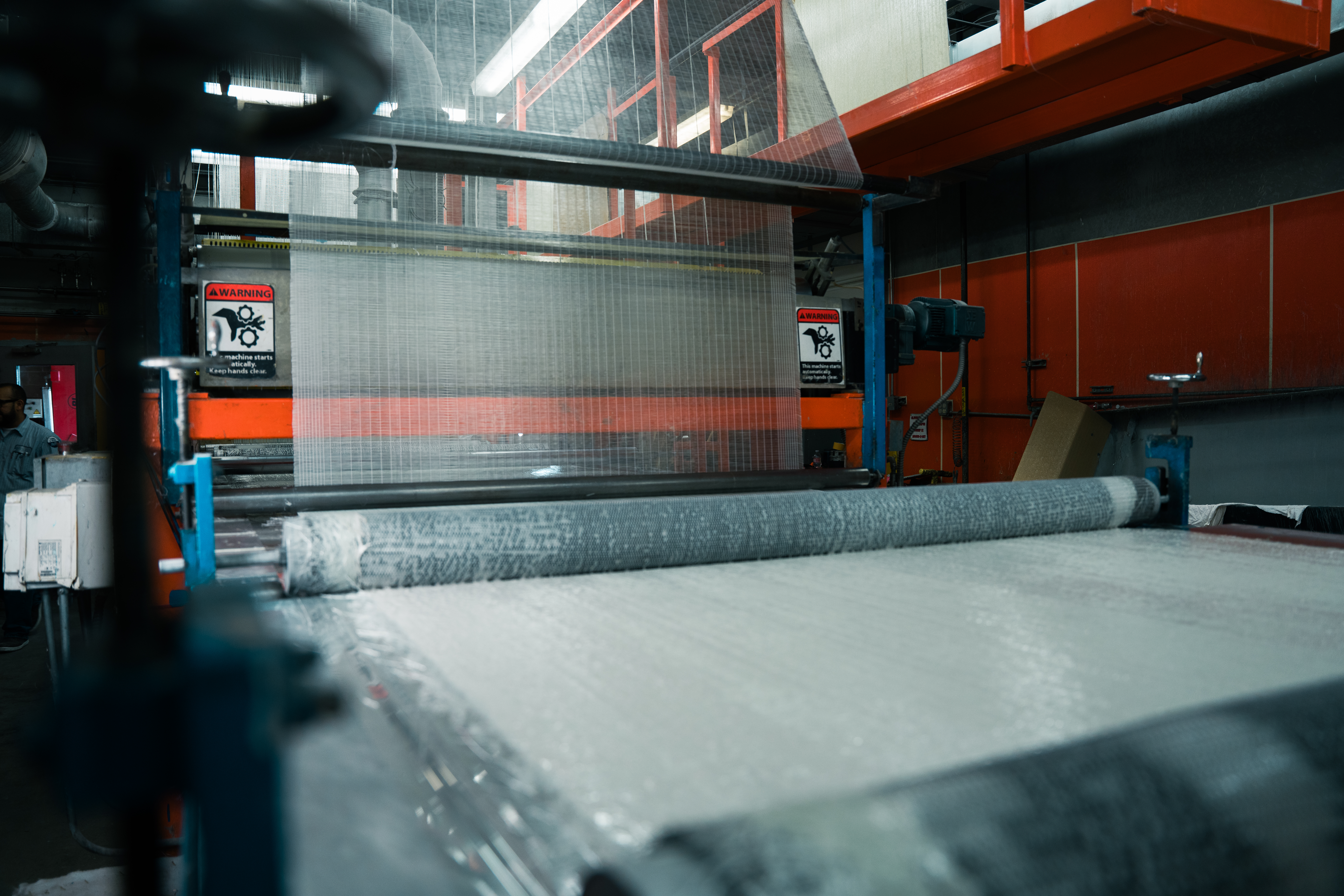