So many industries use fiberglass tanks for storing chemicals and for processing: wastewater, marine, manufacturing, transportation, military applications, and more. It’s easy to customize FRP materials for different applications because there is a range of fabrication options and accessories.
Whether they’ll be used outdoors or indoors, and no matter the size or contents, tanks must be installed and set up carefully to prevent damage and ensure a long useful life. An experienced vendor should be able to work with you and your site, even in tight quarters or challenging locations.
CAREFUL PLANNING AND INSTALLATION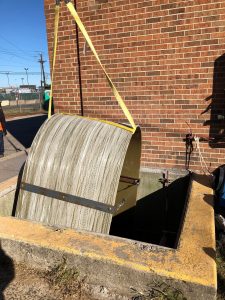
Where there’s a need for a tank, there’s a way to make it happen. This example shows the installation process for three fiberglass tanks that needed to go into a facility’s basement. Because there were limited options for access and maneuvering once inside, the tanks were delivered in pieces with the tops and bottoms cut vertically in two pieces each, separate from the body of the tank.
Pieces were individually lowered into the basement doorway with a hoist. Metal strapping was placed around the tank to stabilize it and prevent damage as it was moved. The fiberglass tanks were assembled in place on prepared concrete pads. The last picture shows how small the space is relative to the size of the tanks and the low ceiling clearance.
TOP TIPS FOR SUCCESSFUL SITE INSTALLATION
Even in less complex installations, there are precautions that help minimize damage. Your vendor should take care to transport the tank and any accessories so they arrive in good condition. Once it arrives keep these tips in mind:
- Be available to inspect the tank and equipment as soon as they arrive so you can note any pre-existing damage, missing equipment, or other problems
- Don’t roll or slide a tank across the ground as this could cause dents, cracks, or crazing. Only lift a tank with designated lifting lugs.
- Avoid causing impact to the tank such as dropping, bumping with tools, or wrapping and pulling or lifting it with chain, all of which can lead to localized cracks or crazing
- Assemble and install tanks on flat, smooth surfaces. Concrete pads are common but a level bed of pea gravel may also work depending on the site.
- Provide adequate support for each support leg on round or cone-shaped bottom tanks, and make sure each leg is level.
- Provide adequate supports for any piping, nozzles, gauges, or other attached accessories.
- Plumb and level the tank before filling it, then check for level again after it’s full.
- Conduct hydrotesting (also called hydrostatic testing) on the tank prior to filling it with its final contents or using it for processing. It tests for leaks, cracks, or other discontinuities in the FRP material, or structural problems. It is also an opportunity to ensure the pad is level and able to support the weight of the tank. The test is usually performed by filling the tank with water and letting it sit for 24 hours or another designated time period, and making periodic observations. Additional mechanical tests may be performed to check the tank at the vendor’s site or your location.
- Use anchor bolts and hold down lugs to secure it to the concrete pad. Tanks often include tie-down points to secure with cables or cord. Avoid making these too tight, which could pull the brackets out of the tank over time.
- Horizontal tanks should be supported with flat metal bands and support saddles to hold them securely in place.
Taking time to plan and execute a careful installation is just as important as expert fabrication. After all, no one wants to erase the hours of effort that went into preparing it in top condition just to cause damage once it’s on-site. If you’re adding tanks to your facility, contact us to learn more.