Composite Decking for Pedestrian Bridges
FRP Pedestrian Bridges are a Mainstay of Parks, Campuses and Urban Architecture
Pedestrian bridges must maintain their non-slip surface when exposed to different environmental conditions, including rain, snow and more severe weather threats; as well as snow clearing equipment.
Pedestrian bridges must be carefully engineered to withstand a range of loadings and types of traffic without experiencing undue wear.
In some cases, this means congested human traffic including fully packed bridges watching holiday events. This is also scooters, bicycles, and skateboards. Larger bridges must handle maintenance vehicles and emergency vehicles when the pedestrian bridge is the quickest path for people's safety. All of which can put additional strain on the bridge, the decking, and its surface.
The Creative Composites Group supplies engineered Fiber-Reinforced Polymer (FRP) decking to ensure that pedestrian bridges hold up to all of these pressures with little to no maintenance required. Our FRP structure is composed of a protective polymer matrix supporting high strength fibers—yielding a lightweight material that is sturdy but comfortable for pedestrians.
We incorporate corrosion-resistant polymers to prevent degradation, leading to long and maintenance-free life cycles. Thanks to these unique construction details, FRP decking is strong, durable, and infinitely adaptable: our decking is compatible with nearly any superstructure configuration and easily incorporates design features like crowns, skews or curbs. A full range of sizes, shapes and depths are available, as are different combinations of strength and stiffness tailored to meet any load requirements.
FRP for Pedestrian Bridges: Emphasizing Function & Safety Concerns
Two main requirements for many pedestrian bridges are shape and safety. While pedestrian paths need to be designed to be non-slip to prevent falls, there are other safety considerations as well. For instance, existing bridges are often converted to pedestrian walkways, but in these cases, the existing structure has already accumulated wear over time. To prevent undue strain on a structure that might already be fragile, the decking design needs to distribute traffic evenly without adding too much unnecessary weight. Widening the path with concrete may be an option for newer structures, but it’s impractical and often completely impossible for aging bridges: the amount of concrete needed for a sufficiently wide path is simply too heavy for decades-old supports to handle.
These safety concerns are especially pronounced with shared-use bridges, which might see any combination of pedestrians and bikers on a given day. A shared-use design warrants extra width to prevent collisions, and it must also support heavier and more variable weights.
Installing an FRP deck addresses all of these concerns for both new and old bridges. When considering a newly designed pathway, high-performance is critical, but so is longevity. FiberSpan™ decking protects your investment with an incredibly durable, corrosion resistant structure that provides for up to 75 years of design life. And because FRP decking is lightweight and flexible, it minimizes stress on the underlying structure, making it ideal for renovations.
Bridge Function Considerations
Whether the bridge structure is to go in a park, across a body of water or around an office building, the shape needs to mesh with the surroundings while still allowing safe passage for the expected level of traffic. Whatever the final form ends up being, an FRP surface is easily customizable to fit both physically and aesthetically. Our FRP decking is suitable for any size, shape or skew.
Thanks to this flexibility, FRP decking is perfect for bridges ranging from short, straight,and level to long, complex and winding. And with custom colors available, the surface will complement the existing environment, so you won’t have to sacrifice appearance for a resilient, performance surface.
Combining Form & Function
At Creative Composites Group, we’re committed to meeting your requirements with precision and professionalism. We’ll work closely with your design team to provide the ideal FRP bridge structure for your project, considering not only weight and safety but also aesthetic traits. We’ve constructed curved decks, cantilevered decks, and decks ranging in size from 600 to 18,000 square feet. No shape is too complex for our talented engineering team, and we execute every project with an eye toward safety and functionality, as we strive to fulfill your specific vision.
Advantages of Using FRP for Pedestrian Bridges:
- Lightweight Construction — An FRP deck weighs at most 20% of a comparable reinforced- concrete design. In addition to reducing strain on the bridge’s structure, this weight reduction is also a substantial advantage in the construction process, allowing for easy, rapid, and affordable installation
- Corrosion-Resistant — FRP surfaces resist degradation from all common corrosive and abrasive influences. Even power-washers or petroleum-based chemicals won’t damage the surface, to say nothing of the UV and weather-resistance inherent to the material
- Maintenance-Free — Reinforced concrete bridges have a standard life span of 15-20 years, especially when exposed to chemicals or harsh weather. But because FRP withstands degradation from those same forces, it has a substantially longer working life. You can expect your FRP deck to last roughly 75 years with no maintenance, even when installed in difficult environmental conditions
- Cost-Effective — Virtually eliminating maintenance comes with a financial incentive, as well. Choosing a durable material that requires no service saves a substantial amount in the long run, considering both labor and material costs
- Design Flexibility — FRP can be engineered with ideal structural properties to match almost any load. We also offer our FRP material in customizable panels, which allows easy installation regardless of bridge shape or size
Composite Decking Product Options
Heavy Duty Planking
Heavy Duty Planking designed to mimic and replace wood timbers. This product is cost effective choice for short span bridges with constant thickness decking. HD Planking is a pultruded profile that can be installed just like wood planks. LEARN MORE>>
Molded FiberSpan™ Panels
Molded FiberSpan panels for larger bridges incorporating design shapes and functional features such as crown, cross-slope, curbs and drainage systems.
The large, pre-fabricated FiberSpan panels are a sandwich structure construction for maximum design flexibility to meet all loading requirements and support conditions. There is a fiber-reinforced foam core enclosed within two fiberglass facesheets to create the sandwich structure. The fibers of the internal webbing are packed tightly together and oriented at ± 45° angles, which, taken together, allows for maximum shear properties and crush resistance. We use a closed-cell foam to create the shape and eliminate open cavities where water could collect.
The decking panels provide strength to handle a uniform load of 90 psf for all designs, complying with regulatory standards for pedestrian bridges (per the American Association of State Highway and Transportation Officials, or AASHTO). Concentrated wheel loads are reacted by the internal webs, supporting emergency vehicle access where necessary. Individual span limits based on superstructure support vary depending on L/D deflection criteria.
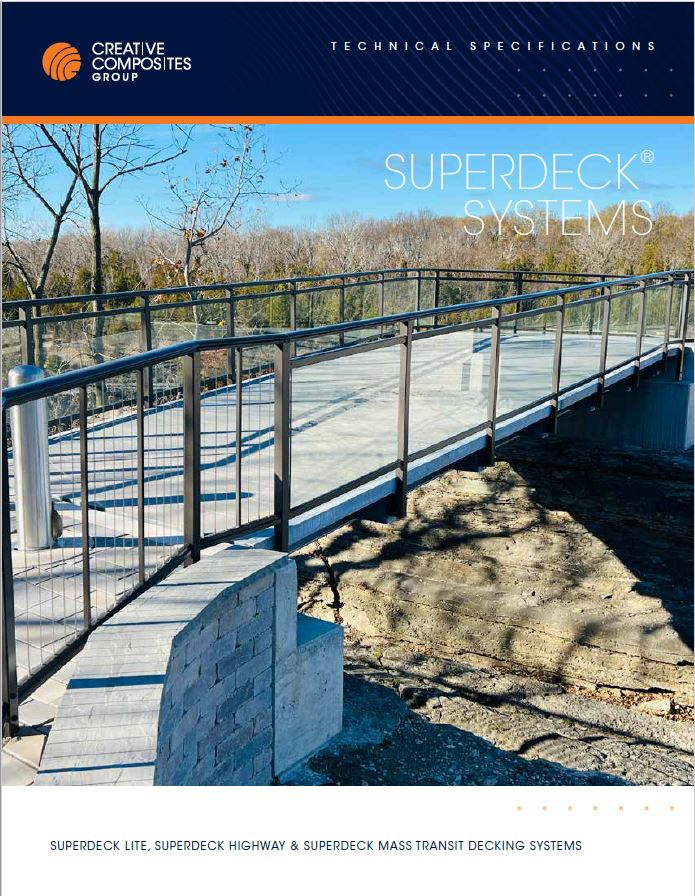
More resources
Learn more about pedestrian bridge deckingBedford Joint Municipal Authority
Related Videos
Frequently Asked Questions
All FAQs-
The only limitation is being able to ship the panels to your site. There are no shape limitations. We do both straight and curved bridges, as well as crowns. Bridge decks panels are up to 50 ft by 12 ft. Pilings are 100 ft long.
-
FRP Decks can be manufactured with:
- Cross Slope
- Curbs
- Drainage scuppers
- Rail posts connection points
- Non-slip overlay
-
Decks are typically connected to the superstructure supports using mechanically fastened clips that capture the underside of the beam flange. This connection restrains the deck for vertical loads (live, uplift) while allowing for construction tolerances and thermal expansion differences. The clips are sized for compaction against the beam flange. At the clip locations, steel plates are embedded in the deck. Holes are drilled and tapped to provide for easy installation on the bridge. Other methods of connection are available as for bridges with unique requirements.
-
FRP decking can be engineered for desired properties such as stiffness, strength and coefficient of thermal expansion. The range of CTE values for FRP decking is 6.5 to 10.5 x 10^-6 in/in/ᵒF. The critical direction is usually the longitudinal bridge direction with FRP decking on steel stringers. The FRP typically has a CTE of 7.5 x 10^-6 in/in/ᵒF in this direction and is connected to the steel with a CTE of 6 x 10^-6 in/in/ᵒF.
-
FRP bridge decks are designed to the same AASHTO requirements as traditional material decks.
For pedestrian decks, this is 90 psf uniform live load and an H-5 vehicle load (10,000 lb.) for decks up to 10 ft wide; and an H-10 vehicle load of 20,000 lb for decks wider than 10 ft.
For vehicles decks, the fully load semi-tractor trailer requirement of HL-93 or HS-25 is handled.
Special load requirements (such as live load plus snow of 150 psf) can be met since FRP has much design flexibility.
-
There are two options for panel-to-panel joints:
- A foam backing seal with a high elongation sealant on top. The sealant allows for many color options and can match the overlay of the deck.
- The second option is pre-compressed foam and silicone strip that is bonded to the panel edge. This is a product used in parking garages and is long lasting. However, the silicone cap only comes in black. CA includes the required panel-to-panel joint gap size during installation to ensure there is adequate sealant width to handle the thermal movement. The recommended gap is typically 3/8” for pedestrian decks and rail platforms.
-
Expansion joints are necessary at bridge span ends where there are higher amounts of movement (ranging from 1” to 4”). There are two options for expansion joints:
A bonded foam strip which may or may not be covered with an expansion cover plate. A set of steel rails with a neoprene gland. The rail is bolted to one deck panel and slides over the adjacent panel. The thickness of both panels is stepped down in the cover plate area.
-
For safety, a non-slip wear surface overlay is applied in the shop to the top surface of pedestrian decks. The pedestrian version uses a quartz aggregate in a methyl methacrylate polymer. The quartz aggregate comes in a variety of colors and is unaffected by UV radiation and will not fade. Vehicle bridges use an aluminum oxide coating. This is affected by steel snow plow blades. Trail bridges with low traffic use an epoxy grit overlay.
-
The oldest FRP pedestrian deck with a non-slip coating is a bike path in Ohio which was installed in 1998. It is exposed to snow and ice and has not required any repair. Quartz aggregate wear surfaces last 25-50 years depending on the amount and type of traffic they are exposed to. Recoating is generally a cosmetic issue; even if the wear surface is scratched or gouged, there is no structural degradation.
-
The non-slip overlay is available in different grit sizes ranging from light grit for bare foot traffic to coarse grit for vehicle traffic.
-
If scratched or chipped, the wear surface can be filled with new material.
Clean the damaged area by grinding away jagged edges. Wipe with a solvent cleaner to remove dust and oil. Mix the estimated amount of the two-part wear surface. Ensure the correct ratio of part A and part B is used. Trowel the new wear surface on the damaged area. Use a 3/8” nap paint roller to create an even, textured wear surface. Roll over the new wear surface only one or two times. Additional rolling will start pulling the new wear surface off as the material sticks to the roller.
The temperature must be above 60°F to apply the wear surface. The wear surface requires time at temperature without rain to correctly set up. It takes one day at temperatures above 80°F. It takes three days at a temperature of 70°F. It takes five days at a temperature of 60°F.