FIBERGLASS TRUSS BRIDGES
composite bridges for pedestrians, equestrians, bikes and trails
Customers increasingly use Fiberglass Reinforced Polymer (FRP) composite bridges for pedestrian, equestrian, bike, trail and access requirements. We have the right solutions in our standard designs and custom creations. Our E.T. Techtonics brand of fiberglass truss bridges have long been the go-to solution for parks across the United States.
Due to the Nature of our FRP Material, E.T. Techtonics® Fiberglass Truss Bridges Are:
- Long-Lasting
- Low Maintenance
- Lightweight
- Reliable
- Sustainable
- Easy to Assemble
Aesthetically pleasing in natural settings, environmentally friendly, and easy to install, we often supply quality fiberglass pedestrian bridges to national, state and local park agencies.
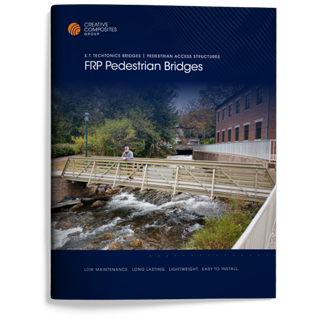
More resources
Learn more about bridgesFRP TRUSS BRIDGES ARE A PERFECT FIT FOR REMOTE LOCATIONS
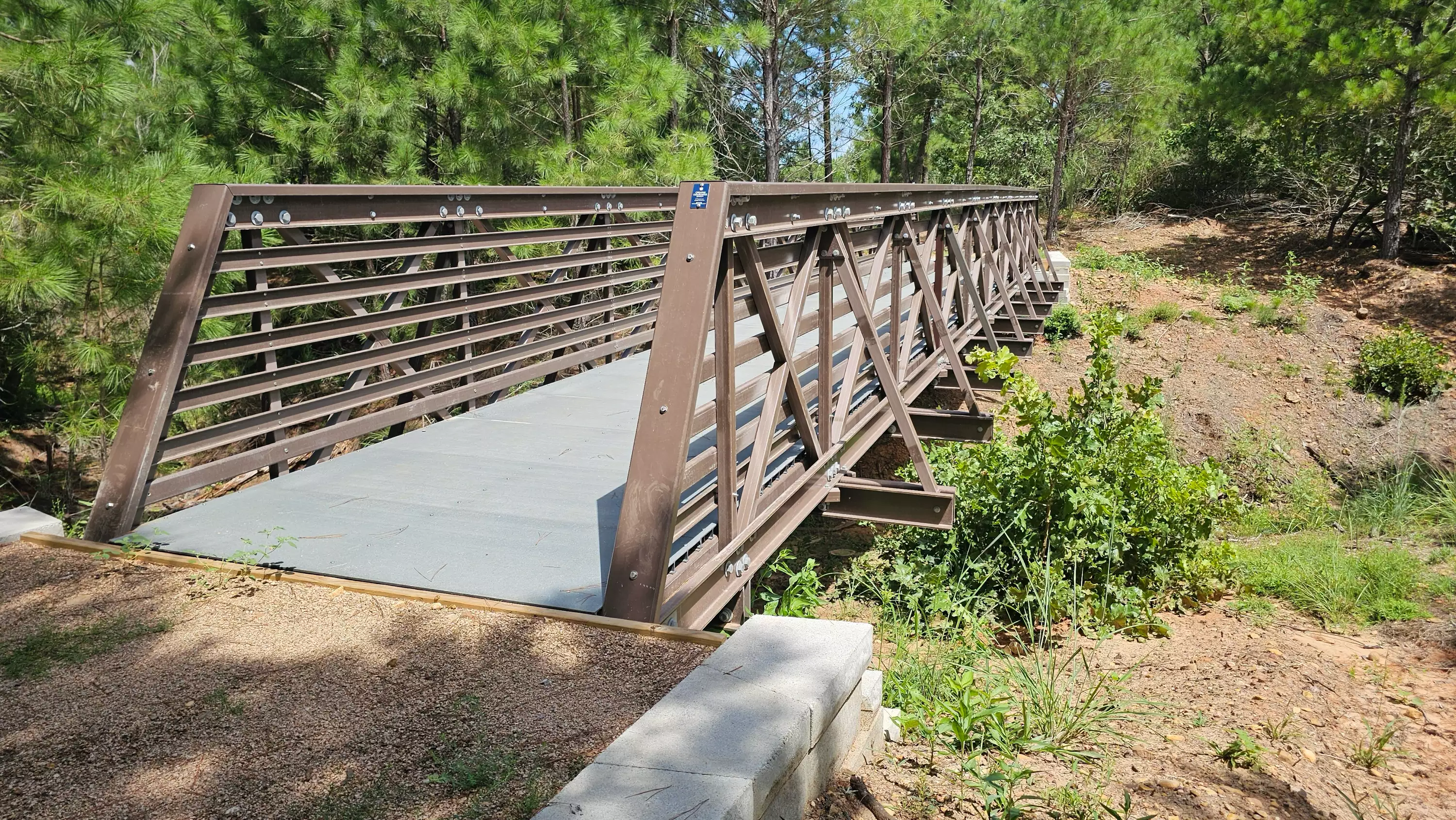
Straight Forward Setup
Designed to be a Match
More Maintanable
Better for the Environment
WHERE TO START?
Let us know your FRP truss bridge needs, including span width and length, and we will help you create a long-lasting solution. Our engineers are equipped to help you design to International Building Code (IBC) and the American Association of State Highway and Transportation Officials (ASHTO) specifications. The structural design of our fiberglass bridges is performed in-house by one of our licensed professional engineers in accordance with recognized engineering practices and principles. We design for uniform live loads, snow loads, vehicle loads, wind loads and seismic loads.
Our team is here to review any questions you might have about FRP truss bridges and assist you with your build.
Related Videos
Frequently Asked Questions
-
Use our free online Request A Quote form to begin the process. Fill in the details and we will work with you to develop an accurate quote for your project. If you prefer, you can visit our contact page to reach us by phone or email. Learn More
-
The schedule from order to delivery is determined on a project by project basis. Use our free online Request A Quote form to give us details about your project. We can put together an estimate for your project that will include scheduling information. Most of our typical spans are shipped within approximately 60 days of order. Learn More
-
CCG does not install these bridges. See our installation guide you can review the different methods of installation. Depending on the type of bridge and the terrain, installation can be performed quickly by a small number of people.
-
E.T. Techtonics park and trail bridges by are typically designed to support pedestrian, bicycle and equestrian uses. They are also often designed to support ATV's, golf carts, and trail maintenance equipment. Our bridges can also be designed for light vehicle applications (10,000 lbs./5T) which includes cars, light pick-up trucks and ambulances. We do not provide vehicular or highway bridges.
-
Components in our bridge system are designed to be hand carried to the site. Usually the heaviest component weighs approximately 90 lbs.
-
Depending on the width the bridge system can be shipped assembled. Most of our clients prefer to have it shipped unassembled as this is the most cost effective approach.
-
Usually we splice bridges over 50'-0" due to shipping. We splice bridges under 50'-0" when requested by the client. Transportation, installation and location typically dictate the most effective component lengths.
-
We have fabricated and shipped 65'-0" long components. Shipping is the major issue and expense when considering components of this length. There is a large cost savings when components of this length are spliced. We recommend splicing.
-
Our longest span to date is 152'.
-
Yes. Note that most cambers require special shop fitting and cambered trusses must be shipped assembled, so this involves additional fabrication costs. Unloading and carrying these assembled trusses may also be more difficult at the jobsite. Assembled trusses for bridges up to 50’-0 in length usually weigh approximately 15 lbs./ft. Bridges over 50’-0 will have spliced truss sections, but due to the heavier components required in the design these sections will weigh approximately 25 lbs./ft. Most of our clients prefer a standard dead load camber only, which can be shipped in component parts for easier transport into remote areas.
-
Standard concrete foundations are typically used with our bridge system. We will provide you a drawing which details the required anchor bolt layout. Anchor bolts can either be cast in place or drilled/epoxied to suit. Clients have also successfully used helical piers with wood or concrete sills, and gabions with wood or concrete sills. We do not provide foundation design, anchor bolts, or soil evaluations. A geotech engineer should be consulted for the foundation design.
-
We have done several bridges of this type. We can discuss the various design options with you and the related costs, if any.
-
In marine type environments and extremely wet environments, we specify stainless steel bolts. We recommend using grade 316SS over 304SS to insure that the fasteners will not exhibit any corrosion.
-
FRP composite decking is available and is ideal for pedestrian bridges located in harsh environments. It is light weight, easy to carry and will withstand the test of time, while providing an ADA compliant slip resistant surface. The most cost-effective decking is standard pressure treated (ACQ) wood. We specify #2 Southern Yellow Pine as this is readily available in our area of the country. We recommend 3"x12" for typical pedestrian and bicycle applications. For equestrian, trail equipment and ATV type applications we use 3"x12". Recycled plastic lumber can also be used as a price point between FRP decking and wood. IPE (hardwood) has been used by our clients on occasions but again at additional cost. Some clients prefer to supply their own deck materials, such as Douglas Fir. For equestrian type applications, we recommend using 3"x12" as horses are sensitive to various textures and sounds of decking.
-
CCG has standardized the spacing at 4". There is no governing standard for trail and park bridge design. For trail bridges the standard maximum opening between horizontal safety midrails is recommended at 9"or less. Typical codes which govern building design recommend a 4"maximum opening for all railings and stairways. Based on this some of our clients specify 4" openings.
-
Fiberglass has similar strength characteristics (tension, compression, bending) to that of steel and aluminum and significantly higher properties in comparison with reinforced concrete and wood. It is 1/5th the weight of steel and 1/2 the weight of aluminum. Its modulus of elasticity is similar to reinforced concrete. Its coefficient of thermal expansion is lower than that of steel and aluminum. Due to its high strength properties it is a viable lightweight alternative to traditional materials of construction with the benefit of being rot and corrosion proof.
-
Fiberglass holds up extremely well in salt air and wet environments and is not affected by termites. Most of our spans, in shady forest locations, exhibit very little change in the appearance of the material over many years. In locations of strong constant sunlight (ultraviolet light) there will be color fading over time, and eventual possible surface deterioration of the material. This does not affect structural performance. We warrant the structural performance of our bridges for 15 years.
-
The fiberglass bridge system is designed to be virtually maintenance-free (a 15-year structural warranty is provided). UV fading will occur over time. The extent is based on the sun's intensity and location.
-
A cable tray made of Fiber Reinforced Polymer (FRP) or Glass Reinforced Polymer (GRP) is an integral part of cable management systems that provides support to electrical cables, protecting them from the harsh environment.
-
Fiberglass cable trays are lightweight and high strength, have flexible installation and can withstand harsh environments making them ideal for cable management systems in challenging conditions faced by industries like chemical plants and construction.
-
Cable trays are a piece of cable management systems that protects cables from heating, corrosive chemicals, the elements, and much more so that your operation may run smoothly. Our cable tray can also reduce shock hazard, provide a non-conductive surface for cable and fitting rusting applications. They are commonly needed in industries like offshore platforms, chemical plants, oil and metal refineries and water treatment plants.
-
You can get an idea of which cable tray will fit your operational needs by downloading our FRP Solutions for Cable Management Systems catalog or by contacting us.
-
We offer a variety of cable trays, all of which are made from high-quality pultruded materials and are extremely durable and resistant to chemical attack. Depending on your needs, cable trays may come in a range of widths and have the possibility to have a solid or slotted bottom as well as a snap-on cover.
-
Cable management systems guarantee secure, consistent data transfer and communication. Enduro’s cable management solutions include fiberglass cable trays, fiberglass ladder type cable trays, fiberglass wireways, fiberglass strut and instrument and pushbutton stands.
-
Industrial cable management ensures performance in industrial spaces, decreases downtime and reduces operational and repair costs. Industrial cable management is a critical support for electrical cables in harsh climates for markets such as mass transit, construction, telecommunication, oil and gas and more.
-
Especially for electricity and data transmission, cable management helps keep facilities and projects safe and running smoothly. Without proper management and protection, cables are susceptible to costly damage that can lead to accidents and downtime.
-
Ladder-type cable trays distribute cables and allow for power distribution throughout facilities such as offshore platforms, chemical plants, oil and metal refineries, and water treatment plants.
-
Typically, cable trays are better suited for lighter weight cable support, instrumentation and tubing. Cable ladder trays often support high-volume and heavy cabling, especially in projects with long spans between supports. Both provide essential cable management and are built to withstand tough conditions.
-
Channel cable trays are a part of cable management systems. This type of cable tray is fully enclosed to protect cables from climate and harsh conditions and are best suited for pneumatic tubing and low-voltage or communications cables.
-
- Petroleum-based chemicals do not degrade or corrode the FRP deck. It will not degrade the non-slip surface, but it may leave a stain.
- De-icing chemicals do not affect FRP.
- There are different grades of polymers used depending on the operation environment.
-
A two-part polyurethane coating is applied to the visible edges and curbs for extra protection to sun and saltwater, to minimize color fading and to match client customer requirements (such as matching the steel color.). The polymer resin has pigments and UV inhibitors as a baseline protection in the deck.
-
Most of the FRP products are manufactured with a fire-resistant polyester or vinyl ester. They have a Class 1 or Class 2 rating per ASTM E84 and a Type 3 rating per NFPA 220, depending on the requirements. The FRP is self-extinguishing and will stop burning once the active flame is removed.
For bridge decking, If there is a large fire on or under the bridge, then steel superstructure deformation becomes a critical issue. Fire resistance has not been an issue for exterior FRP bridge decks and platforms in the past.
If there are additional fire resistance requirements, there are fire proof coating that can be added at an additional cost.
For applications requiring non-combustible materials, a phenolic resin must be used.
-
Yes, FRP deck wear surfaces can be power washed.
-
The resins, coatings, and wear surfaces that we utilize are extremely resistant to UV rays. Direct sunlight exposure does not degrade structural performance. There can be color fading. Polyurethane coatings are often used to eliminate color fading.
-
Fiber Reinforced Polymer (FRP) is a composite material technology that is strong, lightweight, corrosion-resistant and maintenance-free. The material consists of fiber reinforcements surrounded by polymer resins. The fiber reinforcements provide the strength and stiffness to the composite material. The polymer supports the fibers so they can do their job, and protects the fibers from chemicals and UV radiation.
-
- Lightweight—FRP materials are 25% the density of steel. FRP decking is 10% to 20% the weight of reinforced concrete decking, which translates to easy transportation and rapid install.
- Corrosion-resistant—FRP will not degrade because of factors such as snow, ice, salt, or chemicals. Maintenance free—FRP products have a service life of roughly 75 years, during which they require no maintenance. In contrast, reinforced concrete surfaces generally begin to degrade after 15 to 20 years, potentially sooner exposed to heavy chemicals or weather.
- Cost-effective—Due to long service life and zero maintenance costs, FRP products end up costing less than traditional materials.
- Design Flexibility – FRP is an engineered material so the structural properties can be optimized to align with the highest loads.
-
The fiber reinforcements provide the strength and stiffness to the composite material. Fiberglass is the most common reinforcement since it has high strength and good stiffness at a reasonable cost. When higher stiffness is needed for the best weight savings, carbon fiber is used even though it costs more.
-
There are many processes for manufacturing FRP parts. Deciding the right process takes many factors into consideration: size, shape, quantity, production rate, type of fiber and resin, cosmetics, tolerances and cost. Processes include Pultrusion, Vacuum Infusion, Filament Winding and Hand Layup.
-
Applying an FRP liner contributes to the longevity and safety of steel tanks or FRP, water tanks, storage tanks and cooling towers and are not impacted by structural imperfections. The material is lighter weight than metal and concrete but with a very high strength-to-weight ratio, speeding field installation and increasing safety, especially during emergencies. The material is also inherently corrosion-resistant and resists UV degradation.
-
FRP materials are weatherproof, non-corrosive and impact- and fire-resistant, which makes it ideal for harsh industrial conditions. FRP can help ensure durability, safety and optimal performance.
-
Enduro Field Services uses the highest-quality application processes to ensure the highest-quality FRP repairs. First, the application surface is prepared by removing any organic contaminants so that a primer can be applied. The resin is then applied with layers of glass mat and other structural materials. Once the curing process is completed, a final resin coat can be applied. All applications are performed per the customer’s or manufacturer’s specifications with a final inspection to make sure the equipment is ready for use.
-
We have found agencies in the areas that must use de-icing chemicals to ensure safety of their passengers to be very receptive. Concrete deterioration is severely shorting the life of the stations to even just 15 years. And the surface spalling creates a tripping hazard. The corrosion resistance of FRP combined with the ease of installation within hectic train schedules is the combination that garners acceptance. Different agencies have different comfort levels, but we find that showing the advantages, limitations and technical details has been the way to convince the agencies.
-
The anchorage of the platform panels to the support piers using bolted clip connections is similar to the clip connection successfully used for 15 years for FRP pedestrian bridge decking. The biggest issue in the past was using neoprene pad as a shim/interface between FRP and steel or concrete in the first few years. Neoprene is not easy to bond in place. Over time some of the neoprene would slide/vibrate out of position. An interface is not needed on steel supports since both the steel and FRP surfaces are relatively smooth. For the FRP Tee panels, we are attaching UHMW PolyEthylene pads to the expansion end of the FRP panel that sits on concrete piers. This provides a low-friction, abrasive-resistive interface.
-
The standard FRP platform panels are combustible when exposed to a fire source. When the source is removed, the FRP is self-extinguishing. The panels have a Class 1 rating per ASTM E-84 for flame spread testing. The flame spread is slow; allowing passengers time to leave the station and meet egress requirements. There are FRP materials that are non-combustible that CA provides for tunnel applications, but the material costs more than the baseline material.
-
The standard panels are for exterior stations only due to the flame spread and smoke generation.
-
Being a relatively new technology, national standards are not yet in place. The requirements are in special provisions. We have a general specification that we can provide in Word format for customization by designers and agencies. We can also provide examples of the specifications from agencies with FRP platforms in use. Key items are having performance-based requirements to avoid a proprietary spec; and having strong manufacturer qualifications to ensure adequate experience.
-
Yes, the grates are FRP. The grates are ADA compliant.
-
We now use stainless steel for the connection clips and the embedded steel inside the FRP panels. In the past, we used galvanized steel clips on the exterior and embedded carbon steel. Since we are selling 100 year life for FRP, it made sense to use stainless. The cost increase is not much.
-
We have sample performance specifications that we provide as a Word document that the Engineer or owner can edit.
-
A small 3/8 inch by ½ inch drip strip is bonded to the bottom of the panel; just back from the edge. When water runs around the edge of the panel, it hits the strip and cannot wick back to the steel support structure.
-
Your project with CCG starts with a discussion with us to briefly talk through your project and see if FRP will be the right fit. Once you're ready for us to get started on your project, we need your contact information, the dimensions and requirements of the design (drawings are always helpful), how the custom piece will be used, whether the product is currently being made elsewhere and with what materials and any important features or properties this product needs to have. We’ll also need to know whether the product needs any special durability or tolerances (to chemicals, temperatures, etc.). After we receive this information, we can begin working on your custom fiberglass product.
-
Fiberglass offers a unique endurance and durability that isn’t found in many other materials. With a strong tolerance to chemicals and a high strength-to-weight ratio, custom fiberglass products can be cost-effective and the optimum solution for your application. Since every project is unique, the best way to find out if a custom FRP product is right for you is to talk with us.
-
The only limitation is being able to ship the panels to your site. There are no shape limitations. We do both straight and curved bridges, as well as crowns. Bridge decks panels are up to 50 ft by 12 ft. Pilings are 100 ft long.
-
FRP Decks can be manufactured with:
- Cross Slope
- Curbs
- Drainage scuppers
- Rail posts connection points
- Non-slip overlay
-
Decks are typically connected to the superstructure supports using mechanically fastened clips that capture the underside of the beam flange. This connection restrains the deck for vertical loads (live, uplift) while allowing for construction tolerances and thermal expansion differences. The clips are sized for compaction against the beam flange. At the clip locations, steel plates are embedded in the deck. Holes are drilled and tapped to provide for easy installation on the bridge. Other methods of connection are available as for bridges with unique requirements.
-
FRP decking can be engineered for desired properties such as stiffness, strength and coefficient of thermal expansion. The range of CTE values for FRP decking is 6.5 to 10.5 x 10^-6 in/in/ᵒF. The critical direction is usually the longitudinal bridge direction with FRP decking on steel stringers. The FRP typically has a CTE of 7.5 x 10^-6 in/in/ᵒF in this direction and is connected to the steel with a CTE of 6 x 10^-6 in/in/ᵒF.
-
FRP bridge decks are designed to the same AASHTO requirements as traditional material decks.
For pedestrian decks, this is 90 psf uniform live load and an H-5 vehicle load (10,000 lb.) for decks up to 10 ft wide; and an H-10 vehicle load of 20,000 lb for decks wider than 10 ft.
For vehicles decks, the fully load semi-tractor trailer requirement of HL-93 or HS-25 is handled.
Special load requirements (such as live load plus snow of 150 psf) can be met since FRP has much design flexibility.
-
There are two options for panel-to-panel joints:
- A foam backing seal with a high elongation sealant on top. The sealant allows for many color options and can match the overlay of the deck.
- The second option is pre-compressed foam and silicone strip that is bonded to the panel edge. This is a product used in parking garages and is long lasting. However, the silicone cap only comes in black. CA includes the required panel-to-panel joint gap size during installation to ensure there is adequate sealant width to handle the thermal movement. The recommended gap is typically 3/8” for pedestrian decks and rail platforms.
-
Expansion joints are necessary at bridge span ends where there are higher amounts of movement (ranging from 1” to 4”). There are two options for expansion joints:
A bonded foam strip which may or may not be covered with an expansion cover plate. A set of steel rails with a neoprene gland. The rail is bolted to one deck panel and slides over the adjacent panel. The thickness of both panels is stepped down in the cover plate area.
-
For safety, a non-slip wear surface overlay is applied in the shop to the top surface of pedestrian decks. The pedestrian version uses a quartz aggregate in a methyl methacrylate polymer. The quartz aggregate comes in a variety of colors and is unaffected by UV radiation and will not fade. Vehicle bridges use an aluminum oxide coating. This is affected by steel snow plow blades. Trail bridges with low traffic use an epoxy grit overlay.
-
The oldest FRP pedestrian deck with a non-slip coating is a bike path in Ohio which was installed in 1998. It is exposed to snow and ice and has not required any repair. Quartz aggregate wear surfaces last 25-50 years depending on the amount and type of traffic they are exposed to. Recoating is generally a cosmetic issue; even if the wear surface is scratched or gouged, there is no structural degradation.
-
The non-slip overlay is available in different grit sizes ranging from light grit for bare foot traffic to coarse grit for vehicle traffic.
-
If scratched or chipped, the wear surface can be filled with new material.
Clean the damaged area by grinding away jagged edges. Wipe with a solvent cleaner to remove dust and oil. Mix the estimated amount of the two-part wear surface. Ensure the correct ratio of part A and part B is used. Trowel the new wear surface on the damaged area. Use a 3/8” nap paint roller to create an even, textured wear surface. Roll over the new wear surface only one or two times. Additional rolling will start pulling the new wear surface off as the material sticks to the roller.
The temperature must be above 60°F to apply the wear surface. The wear surface requires time at temperature without rain to correctly set up. It takes one day at temperatures above 80°F. It takes three days at a temperature of 70°F. It takes five days at a temperature of 60°F.
-
Pultrusion is a continuous low pressure molding process using fiber reinforcements and thermosetting resins matrices. The fiberglass reinforcements are drawn through a resin bath or injected with resin in which all fibers are thoroughly impregnated with the liquid resin system. The wet-out fiber is formed to the desired geometric shape and pulled into a heated steel die. Once inside the die, the resin cure is initiated by controlling at precise elevated temperatures. The composite laminate solidifies in the exact cavity shape of the die, as it is continuously "pulled" by the pultrusion machine, thus getting the name – Pultrusion.
-
Virtually any constant cross-section can be pultruded dependant upon wall thickness and complexity of the cross-section of the profile.
-
Most commonly utilized resins are standard thermosetting resins such as polyesters, vinyl esters, epoxies, phenolics and urethanes during the pultrusion manufacturing process. However, thermoplastic resins can also be utilized in the Pultrusion process.
-
Typical reinforcements used are fiberglass roving, continuous strand mat, woven and stitched fabrics. Other reinforcing materials such as carbon and aramid fibers, which are more costly, can be utilized during the Pultrusion process to increase the modulus/stiffness of the composite member.
-
For most applications, internal coloration, surfacing veils, and various UV stabilized additives eliminate the need for secondary painting applications. However, to improve the weathering properties or the appearance of a pultruded profile during outdoor exposure, coatings are highly recommended. Most commonly used coatings are Acrylics and Urethanes.
-
The Vacuum Infusion Process uses vacuum pressure to drive resin into a laminate. Materials are laid dry into the mold and the vacuum is applied. Once a strong vacuum is achieved, resin is pushed by atmospheric pressure into the fiber reinforcements via carefully placed tubing and infusion medium. Vacuum infusion greatly improves the fiber-to-resin ratio, and results in a strong, light product. The VIP process is the most cost-effective molding technique for large parts having low to medium quantities.
-
Fiberglass has many qualities that make it ideal for water and wastewater applications:
- Durable and corrosion-resistant, withstanding harsh conditions found in water and wastewater treatment plants
- Lightweight and easy to transport, making it a convenient choice for installation
- Non-conductive, increasing safety in electrical applications
- Easy to clean and maintain, saving money over the life cycle
-
Factors to consider when choosing water and wastewater treatment equipment include the size of the treatment plant, the type of water or wastewater to be treated, the desired level of treatment and budget.
-
To get started with fiberglass water and wastewater treatment equipment, you can contact our team. We can help you choose the right equipment for your needs and provide you with installation and maintenance support.
-
Yes, our water and wastewater products are highly resistant to various chemicals commonly found in treatment facilities, including acids, alkalis and solvents. This makes them ideal for use in corrosive environments where traditional materials like steel or concrete may not hold up over time.
-
Yes, we offer a range of customization options for our water and wastewater products. We work closely with our clients to ensure their specific needs and that the final product meets all applicable regulations and standards.
-
Our water and wastewater products are designed to last decades, even in harsh environments. FRP's inherent corrosion-resistance and durability against UV radiation and other degradation means it requires minimal maintenance and remains in like-new condition far longer than many conventional materials.