COMPOSITE FRP RAIL PLATFORMS
Advanced Composite Platforms for Mass Transit
Fiber Reinforced Polymer (FRP) composite rail platforms give transportation agencies a corrosion-resistant structure that can stand up to weather, de-icing chemicals and high foot traffic at train stations. Lightweight panels can be installed quickly around train schedules, limiting the inconvenience to commuters. CCG's mass transit rail platforms are known for their fast installation as well as being long-lasting. Composite rail platforms are designed to be zero-maintenance structures.
FUNCTIONAL FEATURES FOR FRP RAIL PLATFORMS
In addition to FRP's material advantages, CCG offers a variety of features, including crown or cross-slope surfaces, non-slip polymer overlay, warning tactiles at platform edges, curbs, embedded attachment points, drain scuppers and notch-outs for supplemental structures. Our customizable double tee panels offer tailored design and easy installation for both existing and new structures.
STANDARD FEATURES OF COMPOSITE RAIL PLATFORMS:
- Cross-slope, Curbs, Rail Attachments
- Safe Non-Slip Overlay
- Tactile Warning System
- Americans With Disabilities (ADA) Compliant
- Weight is Less Than 20% of Concrete
DESIGN FLEXIBILITY of FRP Platforms
FRP double tee stems can be customized to meet specific size requirements, such as full-length or transition, similar to dapped end beams for traditional concrete double tees. In addition, designs can be modified for easy integration into existing structures, and specialized triple tees can be manufactured for applications with depth restrictions.
FRP Offers EXCEPTIONAL DURABILITY
Our FRP material is extremely resistant to corrosion, chemicals, and harsh environmental conditions. While concrete can experience significant wear if it's exposed to deicing chemicals, FRP material can easily withstand these compounds, making it ideal for use on platforms and walkways that experience intense weather.
Reduce Risks with FIRE-RESISTANCE
We design our fiberglass rail platforms to reduce risk especially with regards to fire safety. Our FRP materials are manufactured to meet NFPA 130 & ASTM E-84 Class 1 standards for fire resistance.
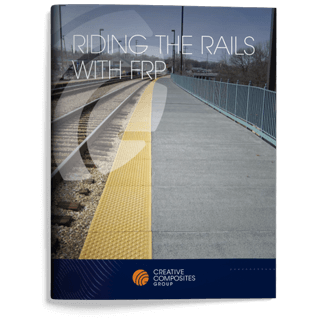
More resources
Learn more about FRP rail platformsRelated Videos
Frequently Asked Questions
All FAQs-
We have found agencies in the areas that must use de-icing chemicals to ensure safety of their passengers to be very receptive. Concrete deterioration is severely shorting the life of the stations to even just 15 years. And the surface spalling creates a tripping hazard. The corrosion resistance of FRP combined with the ease of installation within hectic train schedules is the combination that garners acceptance. Different agencies have different comfort levels, but we find that showing the advantages, limitations and technical details has been the way to convince the agencies.
-
The anchorage of the platform panels to the support piers using bolted clip connections is similar to the clip connection successfully used for 15 years for FRP pedestrian bridge decking. The biggest issue in the past was using neoprene pad as a shim/interface between FRP and steel or concrete in the first few years. Neoprene is not easy to bond in place. Over time some of the neoprene would slide/vibrate out of position. An interface is not needed on steel supports since both the steel and FRP surfaces are relatively smooth. For the FRP Tee panels, we are attaching UHMW PolyEthylene pads to the expansion end of the FRP panel that sits on concrete piers. This provides a low-friction, abrasive-resistive interface.
-
The standard FRP platform panels are combustible when exposed to a fire source. When the source is removed, the FRP is self-extinguishing. The panels have a Class 1 rating per ASTM E-84 for flame spread testing. The flame spread is slow; allowing passengers time to leave the station and meet egress requirements. There are FRP materials that are non-combustible that CA provides for tunnel applications, but the material costs more than the baseline material.
-
The standard panels are for exterior stations only due to the flame spread and smoke generation.
-
Being a relatively new technology, national standards are not yet in place. The requirements are in special provisions. We have a general specification that we can provide in Word format for customization by designers and agencies. We can also provide examples of the specifications from agencies with FRP platforms in use. Key items are having performance-based requirements to avoid a proprietary spec; and having strong manufacturer qualifications to ensure adequate experience.
-
Yes, the grates are FRP. The grates are ADA compliant.
-
We now use stainless steel for the connection clips and the embedded steel inside the FRP panels. In the past, we used galvanized steel clips on the exterior and embedded carbon steel. Since we are selling 100 year life for FRP, it made sense to use stainless. The cost increase is not much.
-
We have sample performance specifications that we provide as a Word document that the Engineer or owner can edit.
-
A small 3/8 inch by ½ inch drip strip is bonded to the bottom of the panel; just back from the edge. When water runs around the edge of the panel, it hits the strip and cannot wick back to the steel support structure.