Filament Winding FRP Manufacturing Process
What is Filament Winding?
The filament winding process wraps resin-soaked fibers around a rotating mandrel to create cylindrical or round composite products with highly customizable strength and performance properties. Filament winding is ideal for creating conduit and bridge drains as well as pressure piping, process piping and vessel lining.
Filament winding allows composites manufacturers to quickly and consistently create shapes that would be difficult or impossible for any other Fiber Reinforced Polymer (FRP) production method. The machinery the manufacturer uses can introduce a high degree of customizability. For example, most machines can change the fiber wrap angle from over 89° to about 30° to deliver desired qualities and can create products ranging from a few inches to up to a dozen feet in diameter.
Steps for Filament Winding
The Filament Winding Process Commonly has Five Steps:
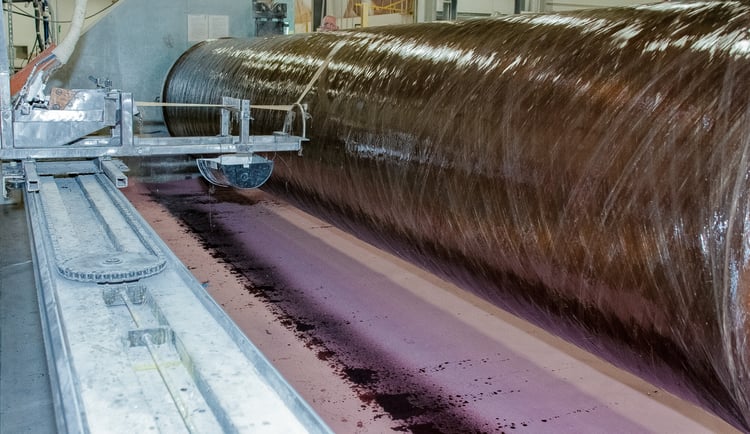
- Mandrel Preparation
- Impregnating Resins
- Fiber Winding
- Curing
- Cooling and Mandrel Removal
A mandrel is a solid shape (like a cylinder) around which the filaments will be wound. There are permanent mandrels and reusable ones. Permanent mandrels will remain inside the final product, while the reusable type will be removed to form a hollow structure. Fibers are saturated with resin as they pass through a bath before being wound onto the rotating mandrel in a specified pattern to yield the desired performance properties. The fully wound piece is then cured with heat. Hollow end-products have the mandrel removed once the product is fully cooled.
FRP Solutions from Creative Composites Group
Creative Composites Group (CCG) is a single-source, U.S. manufacturer of the highest quality FRP solutions. CCG’s in-house expertise in both engineering and design sets us apart and ensures that you get the perfect product for your project’s needs. CCG companies Kenway Composites and United Fiberglass have a combined century of expertise in filament-wound fiberglass products. Partnering with CCG, you’ll get a lasting solution to almost any infrastructural application and the backing of CCG’s expert support.