FRP Pultrusion Process
Fiber Reinforced Pultrusion Process
Pultrusion is a manufacturing process used to create continuous lengths of Fiber Reinforced Polymer (FRP) composites with constant cross-sections. This process is cost-effective and very efficient, making it appealing for use in a wide range of applications. Pultruded composite shapes (profiles) exhibit similar performance characteristics of standard metal shapes, but offer distinct advantages over these materials. Here we discuss how pultrusion works to help you better understand the process and its benefits.
What is Pultrusion?
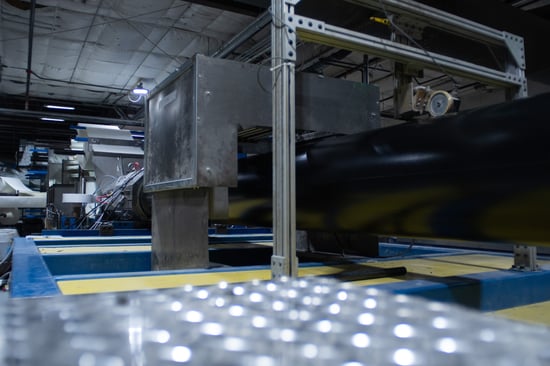
Pultrusion is one of the first composite manufacturing processes developed and has been used since 1951. It has consistently evolved to meet the diverse needs of the industries it serves. This method of manufacturing creates consistent cross-section FRP profiles that closely resemble the steel profiles typically used in construction. It is analogous to extrusion, but this process pulls fiber reinforcement through a die. Pultruded FRP composite sections are used to quickly and easily construct corrosion-resistant, lightweight and electrically non-conductive alternatives to steel structures. Examples of typical uses include decking and planking, structural profiles and plates, bridge components, grating and more.
There are a wide number of reasons why engineers and users may opt for pultruded FRP composites rather than more traditional materials. FRP is lightweight and offers immense flexibility, functioning well as both small components and large infrastructure. In addition to serving the construction and automotive industries, FRP is often the material of choice for applications within the consumer goods, marine, electric and wastewater treatment sectors.
Although FRP can be produced using a variety of manufacturing methods, pultrusion is a popular choice due to its cost-effectiveness, energy efficiency, affordability, eco-friendliness and minimal waste production. It is the best method for situations requiring large quantities of engineered structural products using a rapid production and continuous manufacturing process.
Pultruded FRP Composites Offer an Array of Advantages:
- High strength-to-weight ratio — In pound-for-pound comparisons, this material is stronger than steel but is more lightweight, making it easier to work with and less expensive to transport
- Durability — Pultruded FRP composites are very durable, making them suitable for use in various heavy-duty applications
- Corrosion resistance — Its corrosion resistance allows FRP to withstand chemicals, water, salt and other harsh conditions, making it extremely long-lasting and low-maintenance